Executive Summary
Preventative maintenance (PM) is a proactive approach aimed at preventing equipment failures through regular inspections, maintenance, and repairs.
While PM programs are essential for enhancing equipment longevity, reducing downtime, and optimizing operational efficiency, the effectiveness of these programs depends significantly on their periodic revision.
This white paper outlines the reasons why periodic revision of PM programs is crucial, highlighting the benefits of updating maintenance strategies to adapt to evolving operational needs, technological advancements, and data-driven insights.
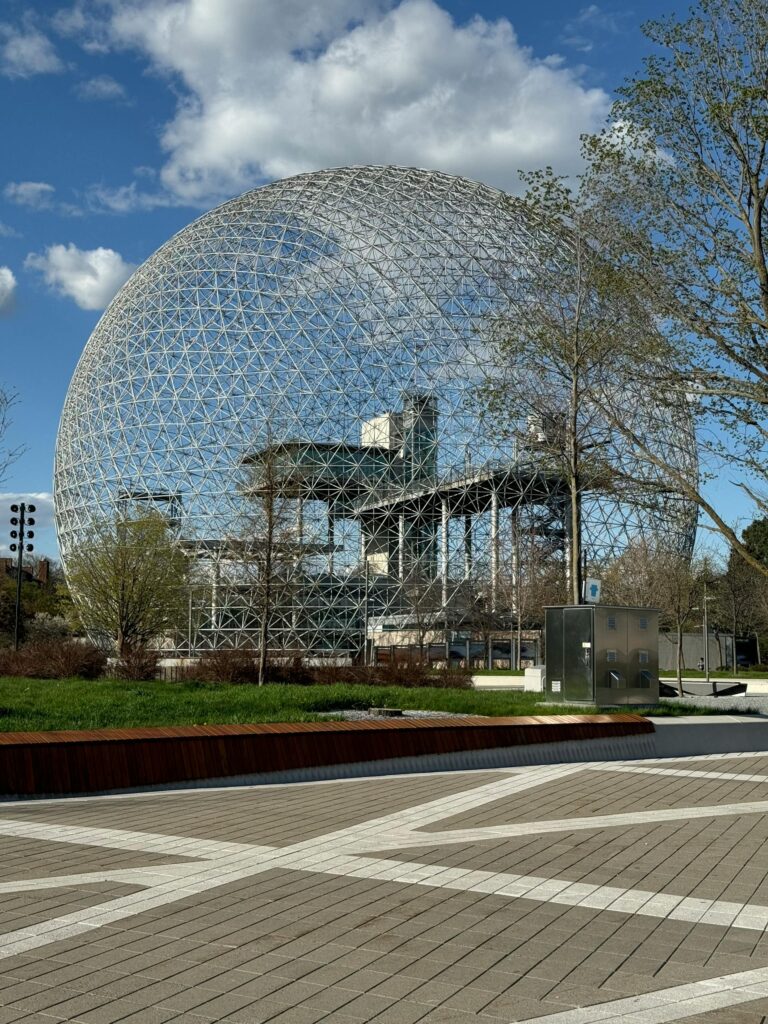
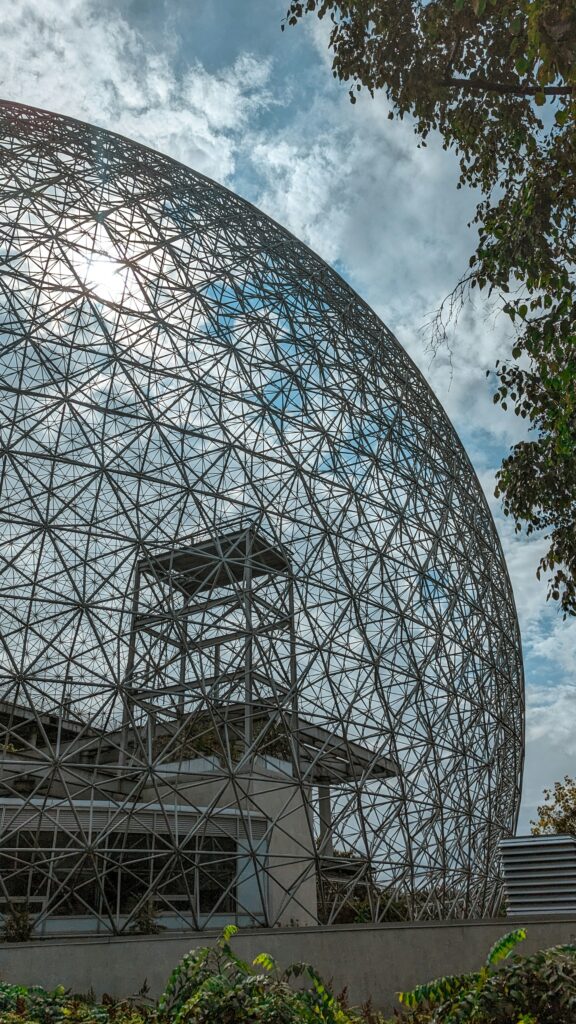
Introduction
Preventative maintenance is designed to maintain equipment and facilities in optimal working condition by conducting routine checks and maintenance activities. However, as operational environments, technologies, and industry standards evolve, so too must the PM programs. Periodic revision ensures that these programs remain relevant, effective, and aligned with current best practices.
The Need for Periodic Revision
1. Adapting to Technological Advancements
Integration of New Technologies: With the rapid pace of technological innovation, new diagnostic tools, sensors, and maintenance techniques become available. Regularly updating PM programs allows organizations to incorporate these advancements, enhancing predictive capabilities and overall efficiency.
Automation and IoT: The advent of the Internet of Things (IoT) and automation technologies has revolutionized maintenance processes. Periodic revisions ensure that PM strategies leverage these technologies for real-time monitoring, data collection, and automated maintenance tasks.
2. Responding to Operational Changes
Shifts in Production Demands: Changes in production volume, product types, or operational schedules can impact equipment usage and wear patterns. Periodic review of PM programs ensures that maintenance activities are adjusted to reflect these changes, preventing over-maintenance or under-maintenance.
Evolving Regulatory Requirements: Compliance with industry regulations and standards is critical. Regular revisions ensure that PM programs remain compliant with the latest regulations, avoiding potential legal and financial repercussions.
3. Incorporating Data-Driven Insights
Historical Maintenance Data: Analysis of historical maintenance data can reveal patterns and trends that inform more effective maintenance schedules. Periodic revisions allow organizations to update their PM programs based on these insights, optimizing maintenance intervals and activities.
Condition-Based Maintenance (CBM): Transitioning from time-based to condition-based maintenance can significantly improve efficiency. Regularly updating PM programs to incorporate CBM strategies ensures that maintenance is performed based on the actual condition of equipment, rather than predetermined intervals.
4. Enhancing Cost Efficiency
Cost-Benefit Analysis: Periodic revisions provide an opportunity to reassess the cost-effectiveness of PM activities. By analyzing the costs and benefits of current maintenance practices, organizations can identify opportunities for cost savings without compromising equipment reliability.
Resource Allocation: Regular updates to PM programs help in optimizing resource allocation, ensuring that maintenance personnel, tools, and spare parts are utilized efficiently.
5. Improving Reliability and Safety
Mitigating Risks: Regular revision of PM programs helps identify potential risks and vulnerabilities in maintenance processes. By addressing these risks proactively, organizations can prevent equipment failures, enhance safety, and reduce the likelihood of accidents.
Continuous Improvement: Maintenance programs should be dynamic, evolving through continuous improvement practices. Periodic revisions encourage a culture of continuous improvement, fostering innovation and adaptation in maintenance strategies.
Best Practices for Periodic Revision
- Scheduled Reviews: Establish a routine schedule for reviewing and updating PM programs, ensuring that revisions are systematic and consistent.
- Stakeholder Involvement: Engage maintenance personnel, engineers, and other stakeholders in the revision process to gather diverse perspectives and insights.
- Data Analysis: Utilize advanced analytics tools to analyze maintenance data and derive actionable insights for program improvements.
- Training and Development: Invest in ongoing training for maintenance staff to ensure they are equipped with the latest skills and knowledge.
- Documentation and Communication: Maintain thorough documentation of all revisions and communicate changes clearly to all relevant parties.
Conclusion:
Periodic revision of preventative maintenance programs is essential for maintaining their effectiveness and relevance in a rapidly changing operational landscape. By regularly updating PM strategies to incorporate new technologies, respond to operational changes, leverage data-driven insights, enhance cost efficiency, and improve reliability and safety, organizations can ensure optimal performance and longevity of their equipment and facilities. Implementing best practices for periodic revision fosters a proactive maintenance culture that drives continuous improvement and operational excellence.
Would you like any adjustments or additions to this white paper?
Images courtesy of Pixabay.